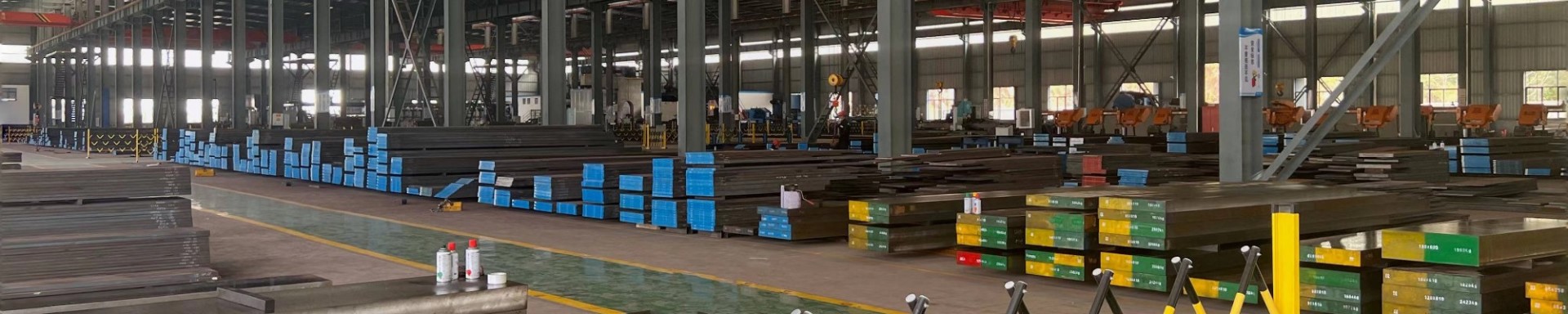
- Home
- >
- Products
- >
- DIN1.2436 Tool Steel
- >
DIN1.2436 Tool Steel
Key Features:
•Superior wear resistance for high-abrasion tasks
•High hardness with retained toughness for shock resistance
•Excellent dimensional stability during hardening
•Ideal for precision cold work tools and dies
- HONGXIN
- 中国
- 30DAYS
- 8000TONS/MONTH
- Information
DIN 1.2436 (AISI D6 / JIS SKD2) Cold Work Tool Steel
1.Overview
DIN 1.2436( ASTM D6 /X210CrW12/JIS SKD2) Tool Steel is a high-carbon, high-chromium cold work tool steel renowned for exceptional wear resistance, high hardness (up to 62-64 HRC), and balanced toughness. Ideal for demanding applications like cold heading dies, blanking tools, and precision cutting blades, DIN 1.2436 excels in environments with severe abrasion and high stress. Its optimized chromium content ensures dimensional stability during heat treatment, while its composition minimizes distortion in complex tool geometries. Widely used in sheet metal processing, automotive tooling, and industrial cutting systems, this steel combines durability with reliability for extended tool life. Available in standard and custom forms, backed by strict quality control for consistent performance.
2.Chemical Composition & Equivalent Grades
Grade | C(%) | Mn(%) | P(%) | S(%) | Si(%) | Cr(%) | W(%) |
DIN1.2436 | 2.00-2.30 | 0.30-0.60 | 0.03 | 0.03 | 0.10-0.40 | 11.00-13.00 | 0.60-0.80 |
ASTM D6 | 2.00-2.20 | 0.20-0.40 | 0.03 | 0.03 | 0.20-0.40 | 11.50-12.50 | 0.60-0.90 |
JIS SKD2 | 2.00-2.30 | 0.30-0.60 | 0.03 | 0.03 | 0.10-0.60 | 11.00-13.00 | 0.60-0.80 |
3.Mechanical & Thermal Properties
Property | Metric Value | Imperial Value |
Hardness | 64-66HRC | |
Compressive Strength | 1320 Mpa | 191,000 psi |
Elastic Modulus | 194 Gpa | 28,100 ksi |
Thermal Conductivity | 20.5 W/m·k | 142 BTU·in/hr·ft²·°F |
Density | 7.67 g/cm³ | 0.277 lb/in³ |
4.Supply Specifications
Size | Round | Dia 12-500mm |
Plate/Flat/Block | Thickness 8mm-300mm | |
Width 210-710mm | ||
Process | EAF+LF+VD+Forged |
5.Heat Treatment Guidelines
Forging
Heat slowly to 700°C and then more rapidly to 900-1050°C. After forging cool slowly, preferably in a furnace.
Annealing
As this grade is supplied in the annealed and machineable condition re-annealing will only be necessary if it has been forged or hardened. Anneal the steel at 800-840℃ and slow furnace cool. Hardness after annealing will be approximately 225HB.
Stress Relieving
When machining operations have been heavy or if the tool has an unbalanced section, remove stresses before hardening by heating up to 650-700℃, equalise, cool slowly.
Hardening
Pre heat slowly to 750-800℃ and soak thoroughly. Continue heating up to the final hardening temperature of 950-980℃, allow the component to be heated through. Cool in air or quench in oil. X210CrW12 is suitable for vacuum (high speed gas) hardening.Tempering
Heat the steel uniformly and thoroughly at the selected tempering temperature and hold for at least one hour per 25mm of total thickness. Double tempering of X210CrW12 should be carried out with intermediate cooling to room temperature.Temperature [℃] 100 200 300 400 500 600 Hardness [HRC] 63 62 60 58 56 48
6.Forging & Machining
Forging: Heat to 900-1050°C; final forging ≥900°C. Light initial blows prevent cracking.
Grinding: Use CBN/diamond tools for optimal surface finish due to high carbide content.
7.Key Applications
Precision Tooling: Blanking dies for ≤2mm sheet metal, thread rolling dies, embossing tools.
Industrial Cutting: Slitting blades, paper/plastic knives, sintered tooling.
Forming Systems: Cold heading dies, press tools, stone molds, hammer cores.
8.Delivery condition
For hot forged or hot rolled bar, usually the delivery condition is hot forged or rolled, annealed, rough turned.
For hot forged plate, usually the delivery condition is hot forged, annealed, milled surface.
For hot rolled plate, usually the delivery condition is hot rolled, annealed, black surface.
9.Production Equipment
Hongxin Mold Tech Co.,Ltd. owns 1 set of Hot Rolling Production Line at size range flats 8-80*210-710mm, rounds 16-50mm Dia.
12 sets of Hydraulic Forging Hammers from Power 560kgs to 6000kgs which could cover flats 40-300*210-710mm.
8sets of EF+LF+VD
5sets of ESR
9sets of Milling Machines
10sets of Turning Lathes
6sets of Precision Milling Machines.
Why Partner With Us?
Global Stock Availability: Rapid delivery of standard and custom sizes.
Certified Quality: Compliance with DIN EN ISO 4957, ASTM A681, and JIS G4404.
Technical Expertise: Full support for heat treatment optimization and tool design.
ISO 9001 Certified: Rigorous quality control ensures consistency and reliability.